Destylacja rozpuszczalników to proces, który polega na oddzieleniu substancji na podstawie różnicy w ich temperaturach wrzenia. Jest to technika szeroko stosowana w chemii, przemyśle farmaceutycznym oraz w produkcji alkoholu. Proces ten zazwyczaj zaczyna się od podgrzewania mieszaniny cieczy, co powoduje, że substancje o niższej temperaturze wrzenia parują jako pierwsze. Opary te są następnie schładzane i skraplane, co pozwala na ich zebranie w postaci cieczy. W przypadku destylacji rozpuszczalników kluczowe jest, aby wybrać odpowiednią aparaturę, taką jak kolumna destylacyjna, która zwiększa efektywność separacji poprzez wielokrotne skraplanie i parowanie. W praktyce oznacza to, że im bardziej różnią się temperatury wrzenia substancji, tym łatwiej jest je oddzielić.
Jakie są rodzaje destylacji rozpuszczalników i ich zastosowania
W dziedzinie destylacji rozpuszczalników wyróżniamy kilka różnych metod, z których każda ma swoje specyficzne zastosowania oraz zalety. Najpopularniejszą formą jest destylacja prosta, która sprawdza się najlepiej w przypadku mieszanin zawierających substancje o znacznie różniących się temperaturach wrzenia. Kolejnym rodzajem jest destylacja frakcyjna, używana do separacji cieczy o zbliżonych temperaturach wrzenia. Dzięki zastosowaniu kolumny frakcyjnej możliwe jest uzyskanie wyższej czystości produktów końcowych. Istnieje także destylacja azeotropowa, która polega na dodawaniu substancji pomocniczych w celu zmiany właściwości mieszaniny i umożliwienia separacji składników azeotropowych. Każda z tych metod znajduje zastosowanie w różnych branżach przemysłowych, od produkcji chemikaliów po przemysł spożywczy.
Jakie są korzyści z wykorzystania destylacji rozpuszczalników
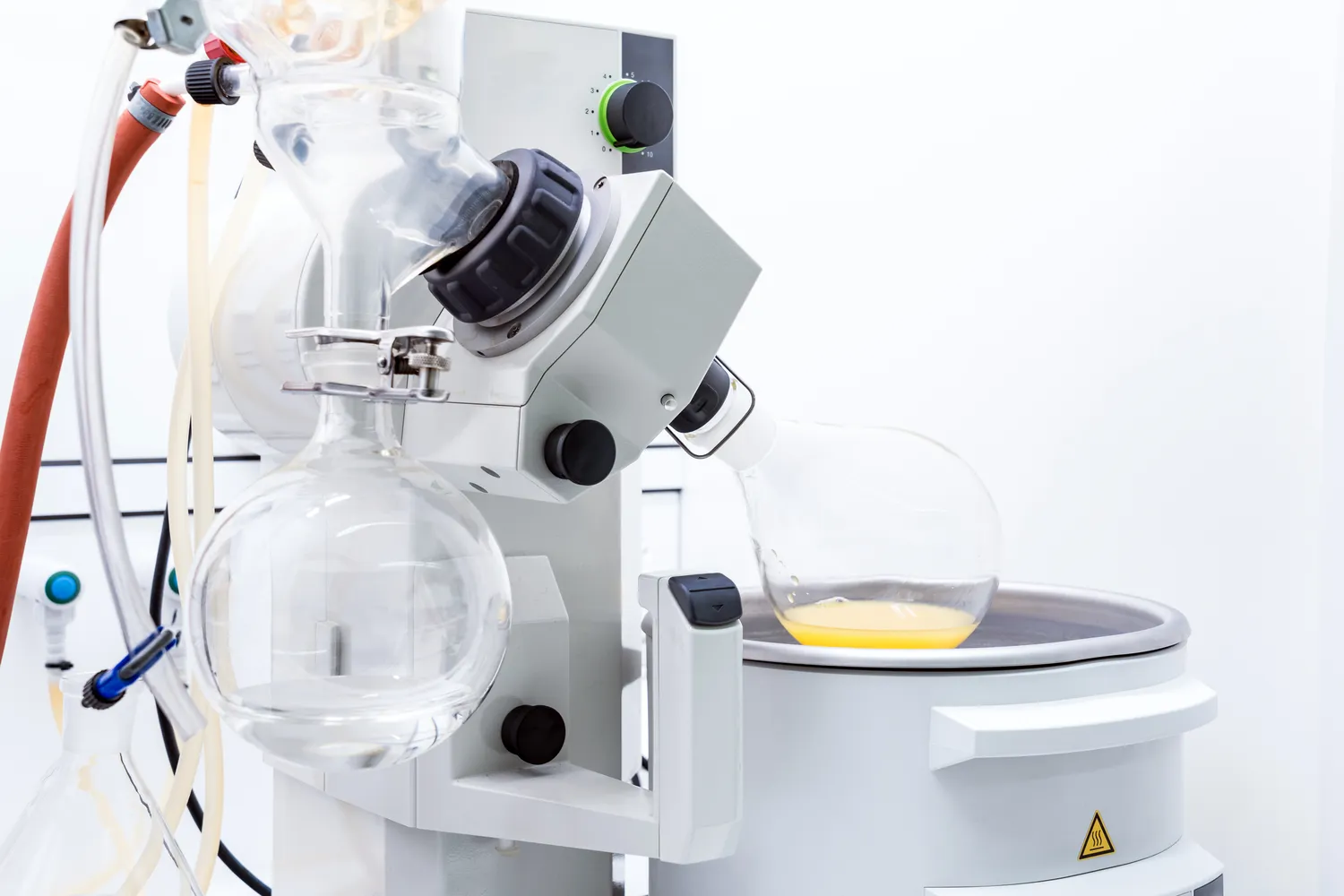
Wykorzystanie destylacji rozpuszczalników niesie ze sobą wiele korzyści zarówno dla przemysłu, jak i dla środowiska. Przede wszystkim proces ten pozwala na efektywne oczyszczanie i recykling rozpuszczalników, co przyczynia się do zmniejszenia ilości odpadów chemicznych. Dzięki temu przedsiębiorstwa mogą obniżyć koszty związane z zakupem nowych surowców oraz zmniejszyć wpływ na środowisko naturalne. Dodatkowo destylacja umożliwia uzyskanie wysokiej czystości produktów końcowych, co jest szczególnie istotne w branżach takich jak farmaceutyka czy chemia analityczna. Kolejną zaletą jest możliwość dostosowania procesu do specyficznych potrzeb produkcyjnych poprzez modyfikację parametrów operacyjnych, takich jak temperatura czy ciśnienie. Warto również zauważyć, że nowoczesne technologie związane z destylacją stają się coraz bardziej zaawansowane, co pozwala na zwiększenie efektywności energetycznej oraz automatyzację procesów produkcyjnych.
Jakie są wyzwania związane z procesem destylacji rozpuszczalników
Mimo licznych korzyści związanych z destylacją rozpuszczalników istnieją także pewne wyzwania i ograniczenia tego procesu. Jednym z głównych problemów jest konieczność precyzyjnego kontrolowania warunków operacyjnych, takich jak temperatura czy ciśnienie. Niewłaściwe ustawienia mogą prowadzić do nieefektywnej separacji lub nawet uszkodzenia sprzętu. Ponadto niektóre mieszaniny mogą tworzyć azeotropy, które utrudniają oddzielanie składników nawet przy użyciu zaawansowanych technik destylacyjnych. Kolejnym wyzwaniem jest zużycie energii – procesy destylacyjne często wymagają dużych nakładów energetycznych, co może wpływać na koszty produkcji oraz ślad węglowy przedsiębiorstw. Wreszcie warto wspomnieć o konieczności przestrzegania rygorystycznych norm bezpieczeństwa i ochrony środowiska podczas przeprowadzania procesów destylacyjnych.
Jakie są najczęstsze zastosowania destylacji rozpuszczalników w przemyśle
Destylacja rozpuszczalników znajduje szerokie zastosowanie w różnych gałęziach przemysłu, co czyni ją kluczowym procesem technologicznym. W przemyśle chemicznym destylacja jest niezbędna do oczyszczania surowców oraz produktów końcowych. Przykładowo, w produkcji chemikaliów organicznych, takich jak alkohole czy ketony, proces ten pozwala na oddzielenie niepożądanych zanieczyszczeń oraz uzyskanie wysokiej czystości substancji. W przemyśle farmaceutycznym destylacja odgrywa kluczową rolę w produkcji leków, gdzie czystość substancji czynnych jest niezwykle istotna dla ich skuteczności i bezpieczeństwa. Kolejnym obszarem zastosowań jest przemysł spożywczy, gdzie destylacja wykorzystywana jest do produkcji alkoholi oraz ekstraktów smakowych. Na przykład, w produkcji whisky czy wina proces destylacji pozwala na uzyskanie pożądanych aromatów i smaków. Wreszcie, destylacja ma także zastosowanie w recyklingu rozpuszczalników, co przyczynia się do zmniejszenia wpływu na środowisko oraz oszczędności surowców.
Jakie są nowoczesne technologie stosowane w destylacji rozpuszczalników
W ostatnich latach rozwój technologii destylacyjnych znacząco wpłynął na efektywność i wydajność tego procesu. Nowoczesne systemy destylacyjne często wykorzystują zaawansowane technologie, takie jak destylacja membranowa czy destylacja z użyciem ultradźwięków. Destylacja membranowa polega na wykorzystaniu specjalnych membran, które selektywnie przepuszczają określone składniki mieszaniny, co pozwala na ich oddzielenie bez konieczności podgrzewania. Ta metoda charakteryzuje się niższym zużyciem energii oraz mniejszymi stratami materiałowymi. Z kolei destylacja ultradźwiękowa wykorzystuje fale dźwiękowe do zwiększenia efektywności separacji składników poprzez intensyfikację procesu parowania. Dodatkowo nowoczesne systemy automatyzacji i monitorowania procesów pozwalają na precyzyjne kontrolowanie warunków operacyjnych, co zwiększa wydajność i bezpieczeństwo pracy. Warto również wspomnieć o zastosowaniu technologii cyfrowych i sztucznej inteligencji w optymalizacji procesów destylacyjnych, co może prowadzić do dalszego zwiększenia efektywności energetycznej oraz redukcji kosztów operacyjnych.
Jakie są różnice między destylacją a innymi metodami separacji
Destylacja jest jedną z wielu metod separacji substancji chemicznych, ale różni się od innych technik pod względem zasad działania oraz zastosowań. Na przykład filtracja to proces mechaniczny, który polega na oddzieleniu ciał stałych od cieczy za pomocą materiału filtracyjnego. Jest to metoda stosunkowo prosta i często używana w laboratoriach do oczyszczania roztworów. Z kolei ekstrakcja to proces polegający na przeniesieniu składników z jednej fazy do drugiej, zazwyczaj przy użyciu rozpuszczalnika. Ekstrakcja może być bardziej efektywna w przypadku substancji o niskich temperaturach wrzenia lub gdy składniki mają różne rozpuszczalności w różnych rozpuszczalnikach. Inną popularną metodą separacji jest chromatografia, która opiera się na różnicach w adsorpcji składników na stałym nośniku. Chromatografia jest szczególnie przydatna w analizach chemicznych oraz w badaniach jakościowych i ilościowych substancji. W przeciwieństwie do tych metod, destylacja opiera się głównie na różnicach temperatur wrzenia i jest szczególnie skuteczna w przypadku cieczy.
Jakie są przyszłe kierunki rozwoju technologii destylacji rozpuszczalników
Przyszłość technologii destylacji rozpuszczalników zapowiada się obiecująco dzięki ciągłemu postępowi naukowemu i technologicznemu. Jednym z kluczowych kierunków rozwoju jest zwiększenie efektywności energetycznej procesów destylacyjnych poprzez zastosowanie odnawialnych źródeł energii oraz nowoczesnych systemów odzysku ciepła. Dzięki tym innowacjom możliwe będzie znaczne obniżenie kosztów operacyjnych oraz zmniejszenie wpływu na środowisko naturalne. Kolejnym ważnym trendem jest automatyzacja procesów produkcyjnych, która pozwala na lepsze zarządzanie parametrami operacyjnymi oraz szybsze reagowanie na zmiany w składzie mieszanin. Rozwój sztucznej inteligencji i uczenia maszynowego może przyczynić się do optymalizacji procesów destylacyjnych poprzez analizę danych i przewidywanie wyników operacyjnych. Ponadto rosnące zainteresowanie zrównoważonym rozwojem skłania przedsiębiorstwa do poszukiwania alternatywnych metod separacji, które mogą uzupełniać tradycyjne techniki destylacyjne.
Jakie są kluczowe czynniki wpływające na efektywność procesu destylacji
Efektywność procesu destylacji rozpuszczalników zależy od wielu czynników, które mogą znacząco wpłynąć na jakość uzyskiwanych produktów końcowych oraz koszty operacyjne. Jednym z najważniejszych elementów jest temperatura wrzenia poszczególnych składników mieszaniny – im większa różnica między nimi, tym łatwiejsze jest ich oddzielanie. Kolejnym istotnym czynnikiem jest ciśnienie atmosferyczne; obniżenie ciśnienia może prowadzić do zmniejszenia temperatury wrzenia substancji, co może być korzystne dla delikatnych składników chemicznych. Również konstrukcja kolumny destylacyjnej ma kluczowe znaczenie dla efektywności procesu – odpowiednia liczba teoretycznych pięter oraz dobór materiału mogą znacząco wpłynąć na jakość separacji. Ważnym aspektem jest także czas trwania procesu; zbyt krótki czas może prowadzić do niepełnej separacji, podczas gdy zbyt długi może powodować straty materiałowe oraz zwiększone zużycie energii.
Jakie są najczęstsze błędy popełniane podczas procesu destylacji
Podczas przeprowadzania procesu destylacji rozpuszczalników istnieje wiele pułapek i błędów, które mogą prowadzić do nieefektywności lub nawet uszkodzenia sprzętu. Jednym z najczęstszych błędów jest niewłaściwe ustawienie temperatury wrzenia lub ciśnienia roboczego; nieodpowiednie parametry mogą prowadzić do niepełnej separacji składników lub ich degradacji termicznej. Innym powszechnym problemem jest brak odpowiedniej kalibracji sprzętu pomiarowego; niedokładne pomiary mogą skutkować błędnymi decyzjami operacyjnymi oraz obniżeniem jakości produktów końcowych. Dodatkowo zaniedbanie konserwacji aparatury może prowadzić do awarii lub spadku wydajności systemu distylacyjnego; regularne przeglądy techniczne są kluczowe dla zapewnienia prawidłowego funkcjonowania urządzeń. Niekiedy operatorzy mogą również ignorować znaczenie analizy składu mieszaniny przed rozpoczęciem procesu; brak wiedzy o właściwościach chemicznych substancji może prowadzić do nieprzewidzianych problemów podczas separacji.