Destylarka do rozpuszczalnika to urządzenie, które wykorzystuje proces destylacji w celu oddzielenia różnych substancji na podstawie ich temperatury wrzenia. W praktyce oznacza to, że gdy mieszanina rozpuszczalników jest podgrzewana, substancje o niższej temperaturze wrzenia parują jako pierwsze, a następnie są skraplane i zbierane w osobnym naczyniu. Taki proces pozwala na uzyskanie czystych frakcji rozpuszczalników, co jest niezwykle istotne w wielu branżach, takich jak chemia, farmacja czy przemysł kosmetyczny. Destylarki mogą być wykorzystywane zarówno w laboratoriach, gdzie precyzyjne oddzielanie substancji jest kluczowe, jak i w przemyśle, gdzie duże ilości rozpuszczalników muszą być oczyszczane. Warto również zauważyć, że nowoczesne destylarki często wyposażone są w systemy automatyzacji, co zwiększa ich efektywność i ułatwia obsługę.
Jakie są najczęstsze rodzaje destylarek do rozpuszczalników
Na rynku dostępnych jest wiele różnych typów destylarek do rozpuszczalników, które różnią się między sobą konstrukcją oraz przeznaczeniem. Najpopularniejsze z nich to destylarki prostokątne oraz cylindryczne. Destylarki prostokątne charakteryzują się większą powierzchnią parowania, co może przyspieszać proces destylacji. Z kolei destylarki cylindryczne są bardziej kompaktowe i łatwiejsze w obsłudze. Innym ważnym rodzajem są destylarki rotacyjne, które wykorzystują obracające się naczynie do efektywnego oddzielania substancji. Tego typu urządzenia znajdują zastosowanie głównie w laboratoriach badawczych oraz w przemyśle chemicznym. Warto również wspomnieć o destylarkach próżniowych, które umożliwiają destylację substancji w obniżonym ciśnieniu, co pozwala na oddzielanie składników o wysokiej temperaturze wrzenia bez ich degradacji.
Jakie materiały są używane do budowy destylarek do rozpuszczalników
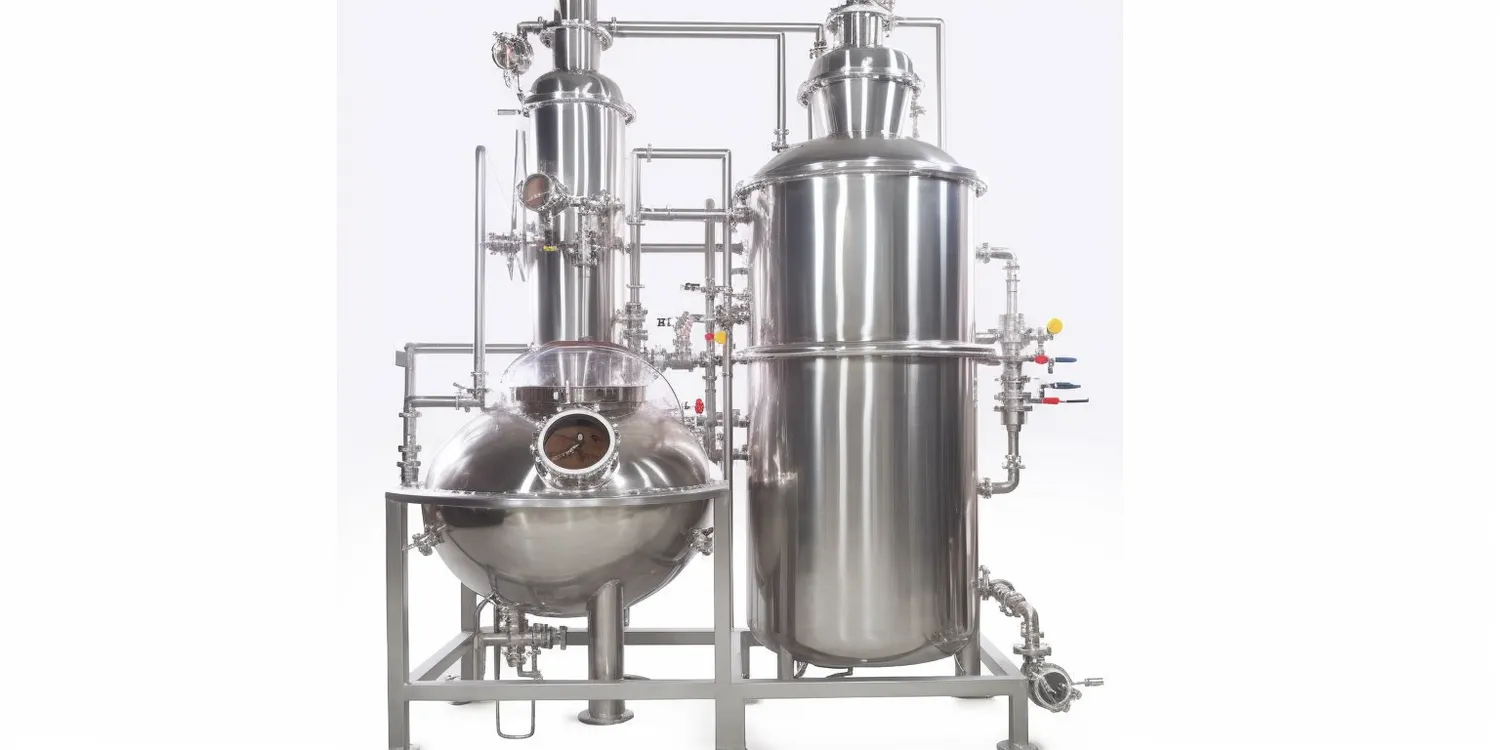
Budowa destylarek do rozpuszczalników wymaga zastosowania materiałów odpornych na działanie chemikaliów oraz wysokich temperatur. Najczęściej wykorzystywanym materiałem jest stal nierdzewna, która charakteryzuje się wysoką odpornością na korozję oraz trwałością. Stal nierdzewna zapewnia również łatwość w utrzymaniu czystości, co jest kluczowe w kontekście pracy z substancjami chemicznymi. W przypadku niektórych elementów destylarek stosuje się także szkło borokrzemowe, które jest odporne na wysokie temperatury oraz działanie większości kwasów i zasad. Szkło borokrzemowe jest szczególnie popularne w laboratoriach ze względu na swoje właściwości optyczne oraz łatwość obserwacji procesu destylacji. Dodatkowo niektóre komponenty mogą być wykonane z tworzyw sztucznych odpornych na działanie chemikaliów, co zwiększa wszechstronność urządzeń.
Jakie są kluczowe czynniki wpływające na wydajność destylarki do rozpuszczalnika
Wydajność destylarki do rozpuszczalnika zależy od wielu czynników, które mogą wpływać na efektywność procesu destylacji. Jednym z najważniejszych aspektów jest temperatura podgrzewania mieszaniny rozpuszczalników. Zbyt niska temperatura może prowadzić do niepełnej separacji składników, podczas gdy zbyt wysoka może powodować ich degradację lub niepożądane reakcje chemiczne. Kolejnym istotnym czynnikiem jest ciśnienie wewnątrz systemu; obniżenie ciśnienia może przyspieszyć proces destylacji poprzez zmniejszenie temperatury wrzenia substancji. Również czas trwania procesu ma znaczenie – odpowiednio dobrany czas może zwiększyć wydajność i jakość uzyskanych frakcji. Nie bez znaczenia jest także konstrukcja samej destylarki; urządzenia o większej powierzchni parowania mogą osiągać lepsze wyniki niż te o mniejszej powierzchni.
Jakie są najczęstsze problemy z destylarkami do rozpuszczalników
Podczas użytkowania destylarek do rozpuszczalników mogą wystąpić różnorodne problemy, które mogą wpływać na jakość i efektywność procesu destylacji. Jednym z najczęstszych problemów jest zatykanie się rurki destylacyjnej, co może prowadzić do obniżenia wydajności urządzenia. Zatykanie może być spowodowane osadami chemicznymi lub zanieczyszczeniami, które gromadzą się w trakcie pracy. Innym powszechnym problemem jest nieodpowiednia temperatura wrzenia, która może wynikać z błędów w ustawieniach urządzenia lub awarii termometru. W takich przypadkach może dojść do niepełnej separacji składników, co skutkuje uzyskaniem nieczystych frakcji. Dodatkowo, niewłaściwe ciśnienie wewnętrzne również może prowadzić do problemów z destylacją; zbyt wysokie ciśnienie może powodować przegrzewanie substancji, a zbyt niskie – spowolnienie procesu. Warto także zwrócić uwagę na uszczelki i połączenia, które mogą ulegać zużyciu i prowadzić do wycieków, co jest nie tylko niebezpieczne, ale także wpływa na efektywność działania destylarki.
Jakie są korzyści z używania destylarki do rozpuszczalnika w przemyśle
Używanie destylarek do rozpuszczalników w przemyśle niesie ze sobą wiele korzyści, które mają kluczowe znaczenie dla efektywności produkcji oraz jakości finalnych produktów. Przede wszystkim, proces destylacji pozwala na uzyskanie czystych frakcji rozpuszczalników, co jest niezwykle istotne w branżach wymagających wysokiej czystości chemicznej, takich jak farmacja czy kosmetyki. Dzięki temu możliwe jest zapewnienie stabilności i bezpieczeństwa produktów końcowych. Kolejną zaletą jest możliwość odzyskiwania rozpuszczalników, co przyczynia się do zmniejszenia kosztów produkcji oraz ograniczenia negatywnego wpływu na środowisko poprzez redukcję odpadów chemicznych. Destylarki umożliwiają również optymalizację procesów produkcyjnych poprzez automatyzację i monitorowanie parametrów pracy, co zwiększa wydajność i precyzję operacji. Dodatkowo, nowoczesne destylarki często wyposażone są w systemy kontroli jakości, które pozwalają na bieżąco monitorować czystość uzyskiwanych frakcji.
Jakie są różnice między destylacją prostą a frakcyjną
Destylacja prosta i frakcyjna to dwa podstawowe rodzaje procesów destylacyjnych, które różnią się między sobą zarówno metodą działania, jak i zastosowaniami. Destylacja prosta polega na jednorazowym podgrzewaniu mieszaniny rozpuszczalników i zbieraniu pary o najniższej temperaturze wrzenia. Ten proces jest stosunkowo prosty i najczęściej wykorzystywany do oddzielania substancji o znacznie różniących się temperaturach wrzenia. Z drugiej strony, destylacja frakcyjna jest bardziej skomplikowanym procesem, który polega na wielokrotnym podgrzewaniu oraz schładzaniu pary w celu uzyskania kilku frakcji o różnych temperaturach wrzenia. Proces ten wykorzystuje kolumny frakcyjne, które zwiększają powierzchnię kontaktu między parą a cieczą, co pozwala na lepsze oddzielanie składników o podobnych temperaturach wrzenia. Destylacja frakcyjna jest szczególnie przydatna w sytuacjach, gdy składniki mają bliskie temperatury wrzenia lub gdy konieczne jest uzyskanie wysokiej czystości produktów końcowych.
Jakie są najlepsze praktyki dotyczące obsługi destylarki do rozpuszczalnika
Aby zapewnić prawidłowe działanie destylarki do rozpuszczalnika oraz maksymalną efektywność procesu destylacji, warto przestrzegać kilku najlepszych praktyk dotyczących jej obsługi. Przede wszystkim kluczowe jest regularne przeprowadzanie konserwacji urządzenia; należy kontrolować stan uszczelek, rur oraz innych elementów konstrukcyjnych pod kątem ewentualnych uszkodzeń czy zużycia. Ważne jest również dbanie o czystość wnętrza destylarki oraz używanych akcesoriów; resztki substancji chemicznych mogą wpływać na jakość procesu oraz prowadzić do kontaminacji uzyskiwanych frakcji. Kolejnym istotnym aspektem jest monitorowanie parametrów pracy urządzenia; regularne sprawdzanie temperatury oraz ciśnienia pozwala na szybką reakcję w przypadku wystąpienia nieprawidłowości. Użytkownicy powinni także zapoznać się z instrukcją obsługi dostarczoną przez producenta oraz stosować się do zaleceń dotyczących bezpieczeństwa pracy z substancjami chemicznymi.
Jakie są koszty zakupu i eksploatacji destylarki do rozpuszczalnika
Koszty zakupu i eksploatacji destylarki do rozpuszczalnika mogą się znacznie różnić w zależności od wielu czynników, takich jak typ urządzenia, jego pojemność oraz dodatkowe funkcje technologiczne. Na rynku dostępne są zarówno proste modele laboratoryjne, których cena może wynosić kilka tysięcy złotych, jak i zaawansowane systemy przemysłowe kosztujące nawet kilkaset tysięcy złotych. Warto zwrócić uwagę na to, że wyższa cena często wiąże się z lepszą jakością wykonania oraz większą wydajnością urządzenia. Koszty eksploatacji obejmują przede wszystkim zużycie energii elektrycznej potrzebnej do podgrzewania mieszaniny oraz ewentualne koszty związane z konserwacją i naprawami urządzenia. Dodatkowo należy uwzględnić wydatki związane z zakupem surowców oraz ich transportem.
Jakie są trendy w technologii destylacji rozpuszczalników
W ostatnich latach można zaobserwować wiele interesujących trendów w technologii destylacji rozpuszczalników, które mają na celu zwiększenie efektywności procesów przemysłowych oraz poprawę jakości uzyskiwanych produktów. Jednym z najważniejszych kierunków rozwoju jest automatyzacja procesów; nowoczesne destylarki często wyposażane są w zaawansowane systemy monitorowania oraz sterowania, które umożliwiają precyzyjne dostosowywanie parametrów pracy do aktualnych potrzeb produkcji. Dzięki temu możliwe jest osiągnięcie wyższej wydajności oraz mniejsze ryzyko błędów ludzkich podczas obsługi urządzeń. Kolejnym trendem jest rosnąca popularność technologii próżniowej; dzięki obniżeniu ciśnienia można przeprowadzać procesy destylacyjne w niższych temperaturach, co pozwala na ochronę delikatnych substancji przed degradacją oraz zwiększenie efektywności separacji składników o bliskich temperaturach wrzenia.