Destylator przemysłowy to urządzenie, które służy do separacji cieczy na podstawie różnicy w temperaturze wrzenia. Proces ten jest kluczowy w wielu branżach, takich jak przemysł chemiczny, farmaceutyczny czy petrochemiczny. Destylacja polega na podgrzewaniu cieczy do momentu, w którym zaczyna ona parować, a następnie schładzaniu pary, aby uzyskać czystą substancję w postaci cieczy. W przemyśle stosuje się różne rodzaje destylatorów, w tym destylatory prostokątne, kolumnowe oraz frakcyjne. Każdy z tych typów ma swoje specyficzne zastosowania oraz zalety. Na przykład destylatory kolumnowe są szczególnie efektywne w separacji mieszanin o bliskich temperaturach wrzenia, co czyni je idealnymi do produkcji wysokiej czystości substancji chemicznych. Warto również zaznaczyć, że proces destylacji może być wspomagany dodatkowymi technikami, takimi jak rektyfikacja, co pozwala na jeszcze dokładniejsze oddzielenie składników.
Jakie są zastosowania destylatorów przemysłowych w różnych branżach
Destylatory przemysłowe znajdują szerokie zastosowanie w wielu branżach, co czyni je niezwykle istotnym elementem nowoczesnej produkcji. W przemyśle chemicznym służą do produkcji różnych substancji chemicznych, takich jak alkohole, kwasy czy rozpuszczalniki. W branży farmaceutycznej destylacja jest kluczowym procesem przy produkcji leków oraz substancji czynnych. Dzięki precyzyjnemu oddzieleniu składników możliwe jest uzyskanie wysokiej jakości produktów farmaceutycznych, które spełniają rygorystyczne normy jakości. W przemyśle petrochemicznym destylatory są używane do rafinacji ropy naftowej, co pozwala na uzyskanie różnych frakcji paliwowych oraz innych produktów naftowych. Ponadto destylatory znajdują zastosowanie w produkcji napojów alkoholowych, gdzie proces destylacji pozwala na uzyskanie wysokoprocentowych trunków z surowców roślinnych.
Jakie są kluczowe elementy konstrukcyjne destylatora przemysłowego
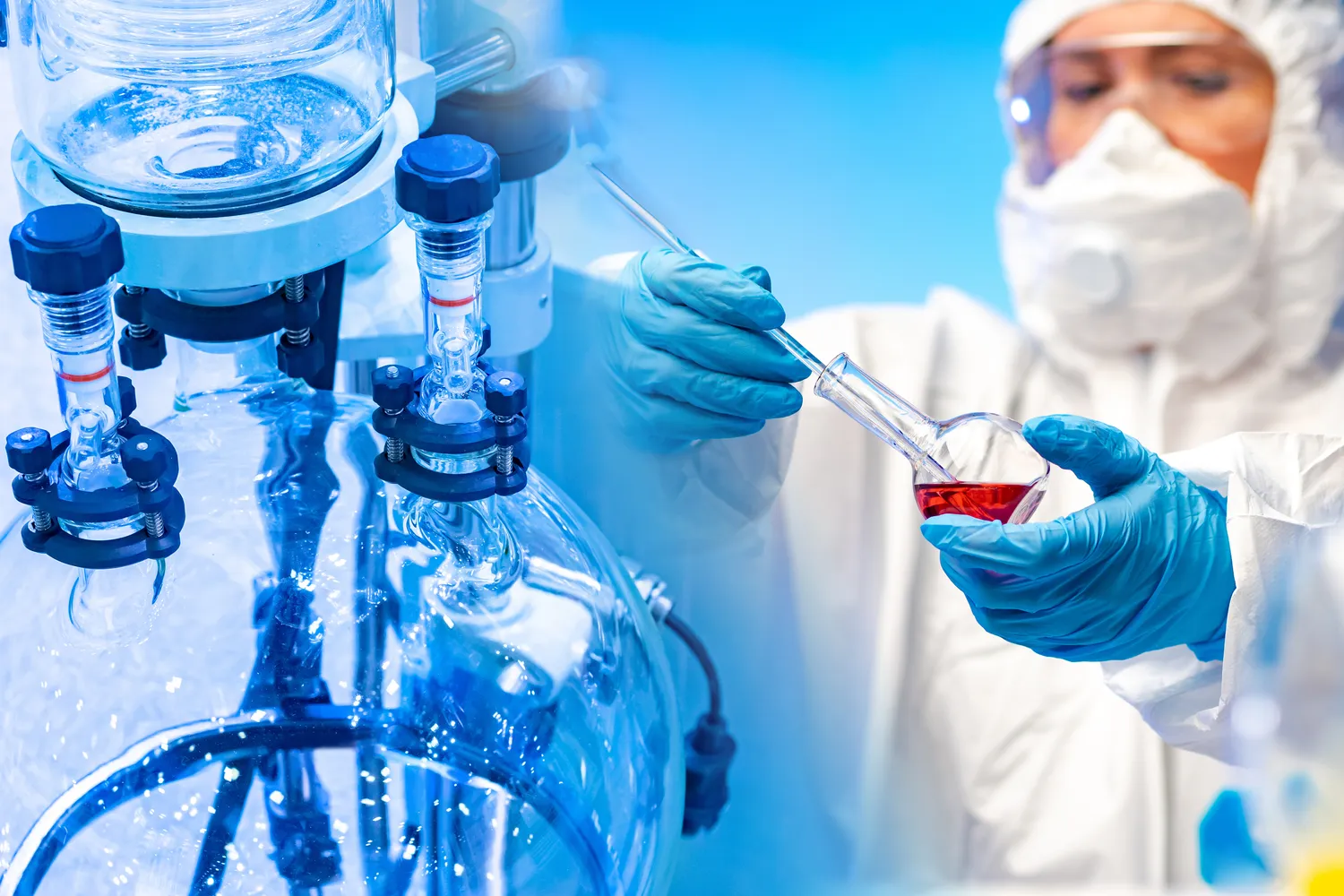
Konstrukcja destylatora przemysłowego składa się z kilku kluczowych elementów, które mają istotny wpływ na efektywność procesu destylacji. Podstawowym elementem jest zbiornik do podgrzewania cieczy, który może być wyposażony w różne źródła ciepła, takie jak elektryczne grzałki czy palniki gazowe. Kolejnym ważnym komponentem jest kolumna destylacyjna, która pełni rolę miejsca separacji składników na podstawie ich temperatur wrzenia. Kolumna ta może być wyposażona w różnego rodzaju packingi lub talerze, które zwiększają powierzchnię kontaktu między parą a cieczą, co poprawia efektywność procesu. Po przejściu przez kolumnę para trafia do skraplacza, gdzie zostaje schłodzona i skroplona z powrotem do postaci cieczy. Dodatkowo nowoczesne destylatory często wyposażone są w systemy automatyki oraz monitoringu, które umożliwiają kontrolowanie parametrów pracy urządzenia oraz optymalizację procesu produkcyjnego.
Jakie są najczęstsze problemy związane z eksploatacją destylatorów przemysłowych
Eksploatacja destylatorów przemysłowych wiąże się z wieloma wyzwaniami i problemami technicznymi, które mogą wpływać na efektywność procesu oraz jakość uzyskiwanych produktów. Jednym z najczęstszych problemów jest osadzanie się zanieczyszczeń wewnątrz kolumny destylacyjnej, co prowadzi do zmniejszenia efektywności separacji składników. Regularne czyszczenie i konserwacja urządzenia są kluczowe dla utrzymania jego wydajności. Innym istotnym zagadnieniem jest kontrola temperatury i ciśnienia w systemie; niewłaściwe ustawienia mogą prowadzić do nieefektywnej separacji lub nawet uszkodzenia sprzętu. Problemy mogą także wynikać z niewłaściwego doboru materiałów surowcowych; niektóre substancje mogą powodować korozję lub inne uszkodzenia elementów konstrukcyjnych. Ponadto awarie systemów automatyki mogą prowadzić do nieprzewidzianych przestojów produkcyjnych oraz strat finansowych dla przedsiębiorstwa.
Jakie są różnice między destylatorami przemysłowymi a laboratoryjnymi
Destylatory przemysłowe i laboratoryjne różnią się znacznie pod względem konstrukcji, zastosowania oraz skali działania. Destylatory przemysłowe są zazwyczaj znacznie większe i bardziej złożone, co pozwala na przetwarzanie dużych ilości surowców w krótkim czasie. W przeciwieństwie do tego, destylatory laboratoryjne są mniejsze i często bardziej przenośne, co sprawia, że są idealne do przeprowadzania eksperymentów oraz badań naukowych. W laboratoriach destylacja jest często stosowana do uzyskiwania czystych substancji chemicznych w małych ilościach, co wymaga precyzyjnego kontrolowania warunków procesu. W przemyśle natomiast kluczowe jest osiągnięcie wysokiej wydajności oraz optymalizacja kosztów produkcji. Kolejną istotną różnicą jest rodzaj używanych materiałów; w laboratoriach często korzysta się z szkła, które umożliwia łatwe obserwowanie procesów, podczas gdy w przemyśle dominują materiały metalowe, odporne na działanie wysokich temperatur oraz agresywnych substancji chemicznych.
Jakie są najnowsze technologie w dziedzinie destylacji przemysłowej
W ostatnich latach w dziedzinie destylacji przemysłowej pojawiło się wiele innowacyjnych technologii, które znacząco poprawiają efektywność procesów oraz jakość uzyskiwanych produktów. Jednym z najważniejszych trendów jest rozwój destylacji membranowej, która wykorzystuje specjalne membrany do separacji składników na poziomie molekularnym. Ta metoda pozwala na oszczędność energii oraz redukcję emisji zanieczyszczeń. Innym interesującym rozwiązaniem jest zastosowanie technologii mikrofalowej, która umożliwia szybkie podgrzewanie cieczy i przyspiesza proces destylacji. Dzięki temu możliwe jest uzyskanie wyższej wydajności oraz lepszej jakości produktów końcowych. Warto również zwrócić uwagę na rozwój systemów automatyzacji i monitoringu, które pozwalają na zdalne zarządzanie procesem destylacji oraz szybką reakcję na ewentualne problemy. Coraz więcej firm inwestuje także w technologie związane z odzyskiem ciepła, co przyczynia się do zmniejszenia zużycia energii oraz obniżenia kosztów produkcji.
Jakie są koszty eksploatacji destylatorów przemysłowych
Koszty eksploatacji destylatorów przemysłowych mogą być znaczne i obejmują wiele różnych aspektów. Pierwszym z nich są koszty zakupu samego urządzenia, które mogą się różnić w zależności od jego wielkości, rodzaju oraz zastosowania. Następnie należy uwzględnić koszty energii potrzebnej do podgrzewania cieczy; w przypadku dużych instalacji przemysłowych zużycie energii może stanowić znaczną część całkowitych kosztów operacyjnych. Kolejnym istotnym elementem są koszty związane z konserwacją i naprawami urządzenia; regularne przeglądy techniczne oraz wymiana zużytych części są niezbędne dla utrzymania efektywności procesu. Koszty surowców również mają duże znaczenie; ceny materiałów mogą się zmieniać w zależności od rynku i dostępności surowców. Dodatkowo warto pamiętać o kosztach związanych z przestrzeganiem norm środowiskowych oraz bezpieczeństwa pracy; wiele krajów wymaga od przedsiębiorstw wdrożenia odpowiednich procedur i systemów zarządzania jakością, co wiąże się z dodatkowymi wydatkami.
Jakie są najważniejsze czynniki wpływające na wybór destylatora przemysłowego
Wybór odpowiedniego destylatora przemysłowego to kluczowy krok dla każdej firmy zajmującej się procesami separacyjnymi. Istnieje wiele czynników, które należy wziąć pod uwagę przy podejmowaniu decyzji o zakupie takiego urządzenia. Pierwszym z nich jest rodzaj przetwarzanej cieczy oraz jej właściwości fizykochemiczne; różne substancje wymagają różnych rozwiązań technologicznych, aby osiągnąć optymalne wyniki separacji. Kolejnym istotnym czynnikiem jest wydajność urządzenia; należy określić, ile surowca będzie przetwarzane w danym czasie oraz jakie parametry jakościowe muszą być spełnione przez uzyskany produkt końcowy. Koszt zakupu i eksploatacji również odgrywa kluczową rolę; przedsiębiorstwa muszą ocenić swoje możliwości finansowe oraz przewidywane koszty operacyjne związane z użytkowaniem destylatora. Ważnym aspektem jest także dostępność serwisu technicznego oraz wsparcia posprzedażowego; wybór renomowanego producenta może zapewnić długoterminową współpracę oraz pomoc w razie awarii urządzenia.
Jakie są przyszłe kierunki rozwoju technologii destylacyjnych
Przemysłowa technologia destylacyjna stoi przed wieloma wyzwaniami i możliwościami rozwoju w nadchodzących latach. Jednym z głównych kierunków rozwoju jest zwiększenie efektywności energetycznej procesów destylacyjnych poprzez zastosowanie nowoczesnych technologii odzysku ciepła oraz alternatywnych źródeł energii, takich jak energia słoneczna czy geotermalna. W miarę rosnącej świadomości ekologicznej przedsiębiorstw coraz większy nacisk kładzie się na minimalizację wpływu procesów produkcyjnych na środowisko naturalne; technologie umożliwiające recykling odpadów czy ograniczenie emisji gazów cieplarnianych będą miały kluczowe znaczenie dla przyszłości branży. Również rozwój automatyzacji i cyfryzacji procesów produkcyjnych staje się nieodłącznym elementem nowoczesnych zakładów przemysłowych; inteligentne systemy monitorujące będą pozwalały na bieżąco analizować dane dotyczące pracy urządzeń i optymalizować procesy produkcyjne w czasie rzeczywistym.
Jakie są wymagania prawne dotyczące użytkowania destylatorów przemysłowych
Użytkowanie destylatorów przemysłowych wiąże się z szeregiem wymagań prawnych, które mają na celu zapewnienie bezpieczeństwa pracy oraz ochrony środowiska naturalnego. Przedsiębiorstwa muszą przestrzegać norm dotyczących emisji zanieczyszczeń do atmosfery oraz odpadów generowanych podczas procesu produkcji; wiele krajów posiada szczegółowe regulacje dotyczące maksymalnych dopuszczalnych wartości emisji substancji szkodliwych. Ponadto konieczne jest uzyskanie odpowiednich zezwoleń na prowadzenie działalności związanej z przetwarzaniem substancji chemicznych; procedury te mogą obejmować zarówno ocenę ryzyka dla zdrowia ludzi, jak i wpływu na środowisko naturalne. Wiele państw wymaga także regularnego przeprowadzania audytów bezpieczeństwa pracy oraz inspekcji technicznych urządzeń; takie działania mają na celu minimalizację ryzyka wystąpienia awarii lub incydentów związanych z użytkowaniem sprzętu. Przedsiębiorstwa powinny również zadbać o szkolenie pracowników obsługujących destylatory, aby zapewnić im wiedzę niezbędną do bezpiecznego wykonywania swoich obowiązków.